What Does it Take to Build the Factory of The Future?
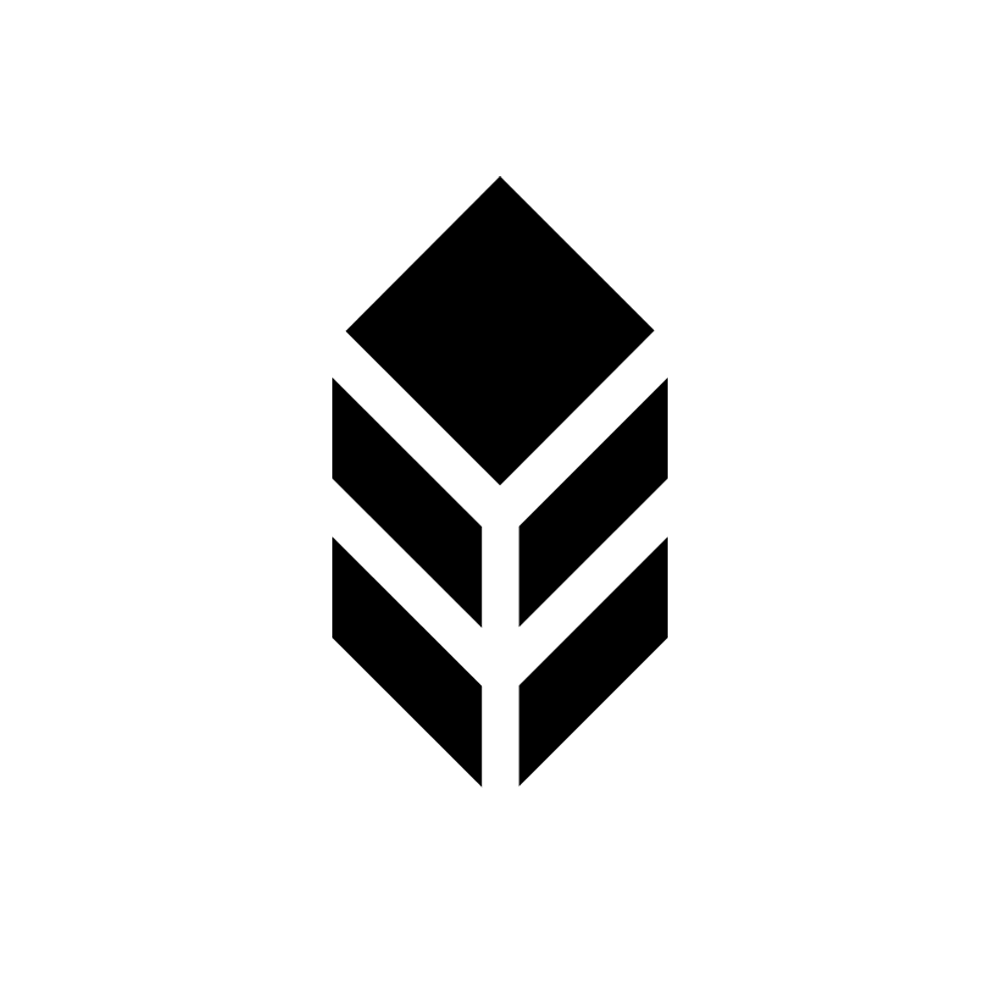
Dan Webb
/
8.28.23
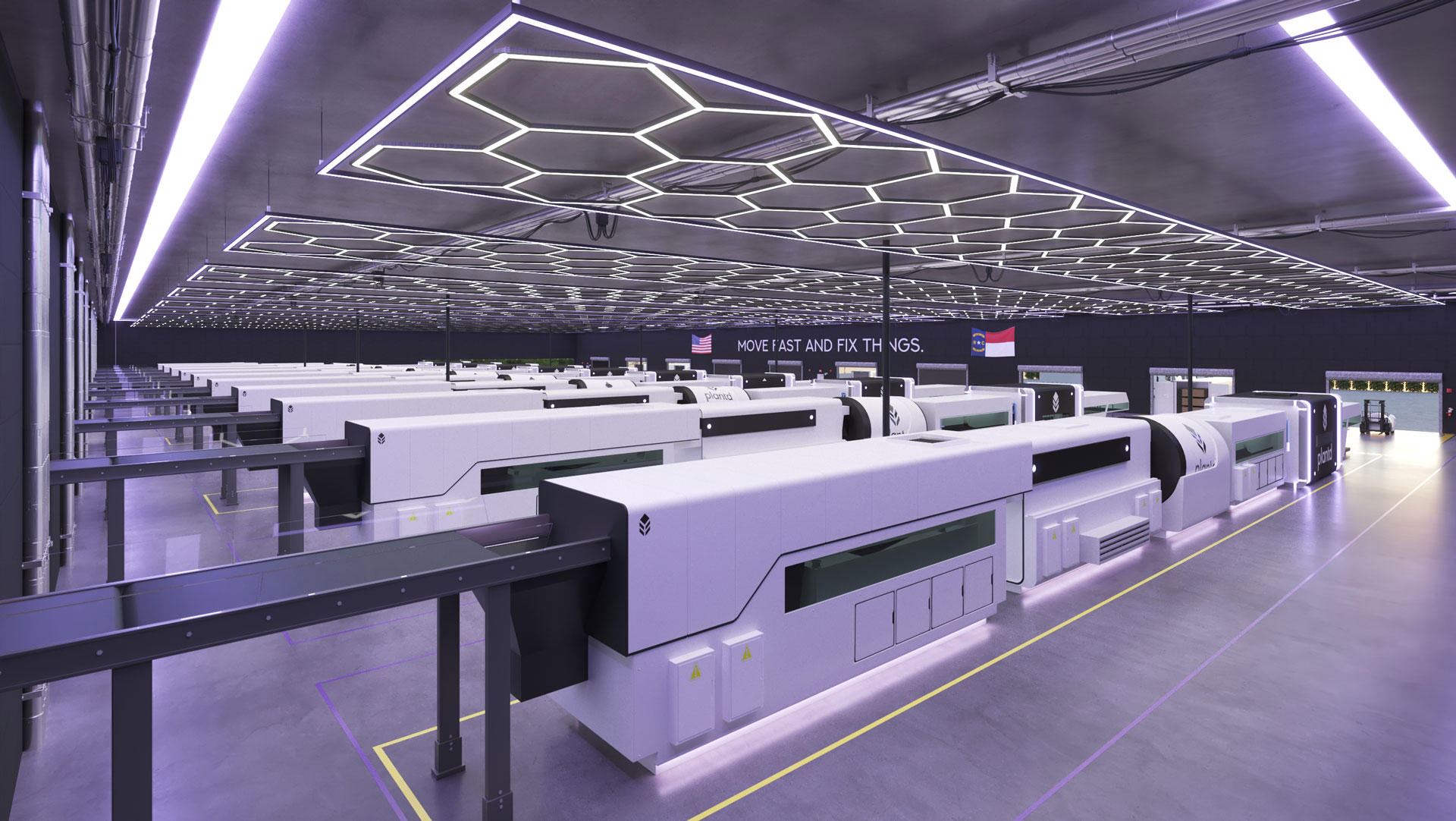
Meet Plantd’s ex-SpaceX Co-Founders
Meet Nathan Silvernail and Huade Tan. This duo previously worked together at SpaceX, where they collaborated to design and build life support systems for spaceships.
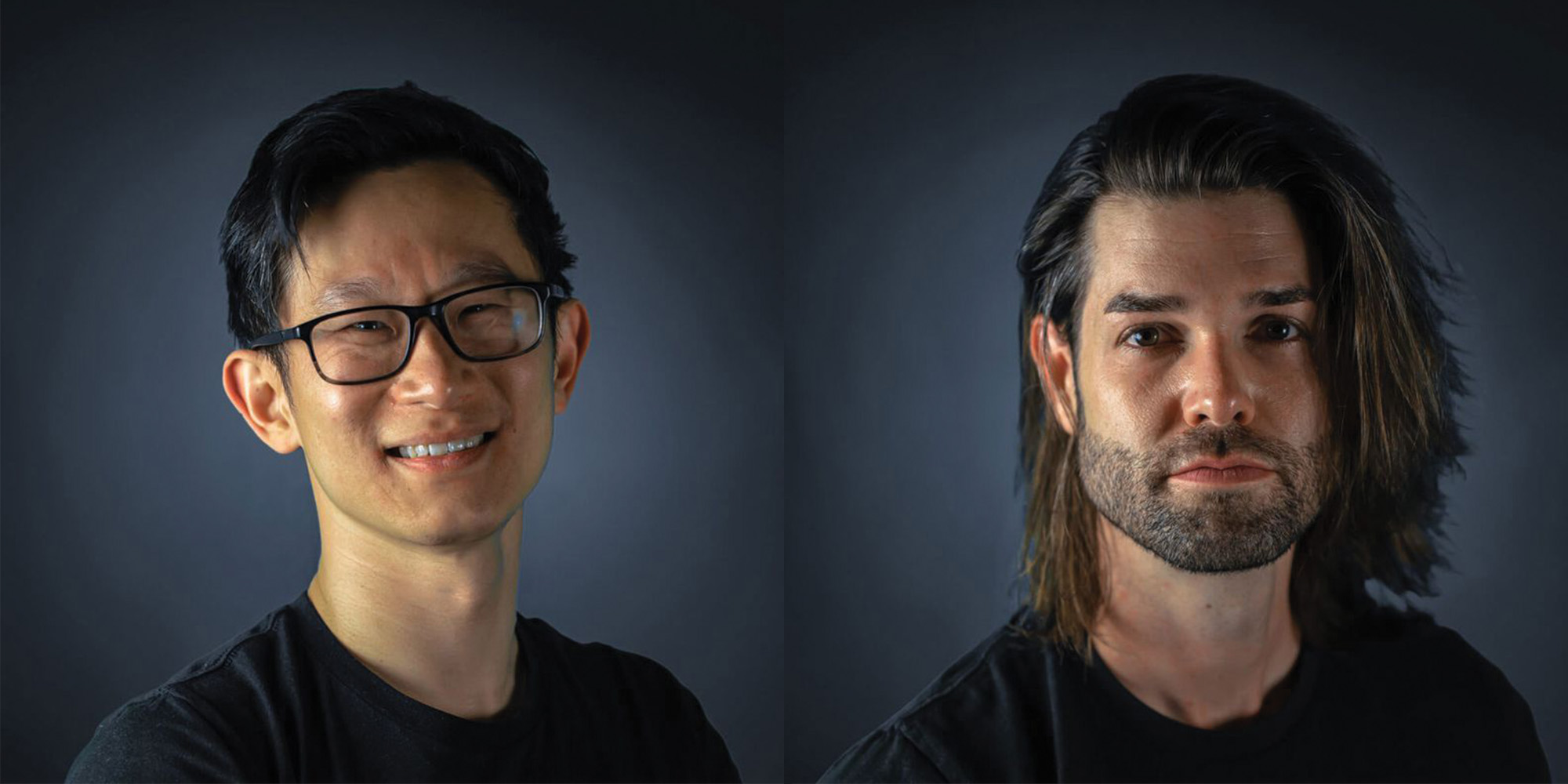
Huade designed the schematics for life support components, while Nathan managed the manufacturing process and flow of parts and materials necessary to bring designs to reality.
Now, as the CTO of Plantd, Huade is leading the Plantd Engineering team toward designing fundamentally new machines to maximize the amount of atmospheric carbon captured in Plantd’s building products. And as Chief Operating Officer, Nathan is responsible for not only the operations of assembling and running these machines but also architecting a new agricultural supply chain for building materials.
Together, they are the heads of the engineering and operations teams that collectively work to build out Plantd’s Factory of the Future and agricultural supply chain.
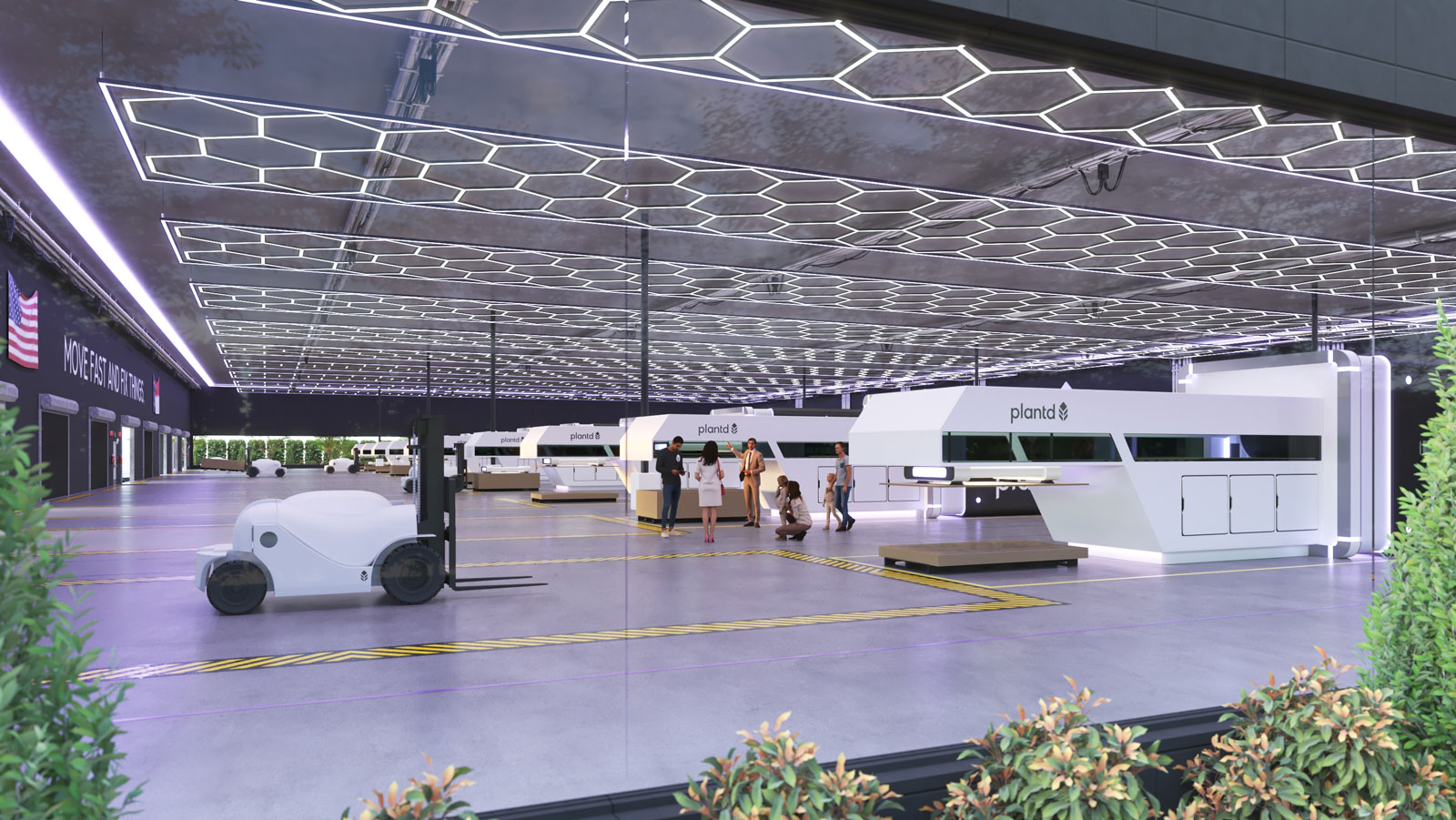
Q: What is Plantd’s production technology?
Huade: All we do is take biomass off the field and lock it away into a durable state for as little energy and as few tons of CO2 emissions as possible. Plantd is unique in how we approach our goals. We are not constrained by existing hardware–– we design things where needed and buy things when available to reach the objective.
Nathan: Plantd’s production technology changes the mindset of the entire industry. We’re optimizing for efficiency all the way around. Production, logistical, and financial efficiencies are all created by redesigning engineered lumber production with a first principles approach.
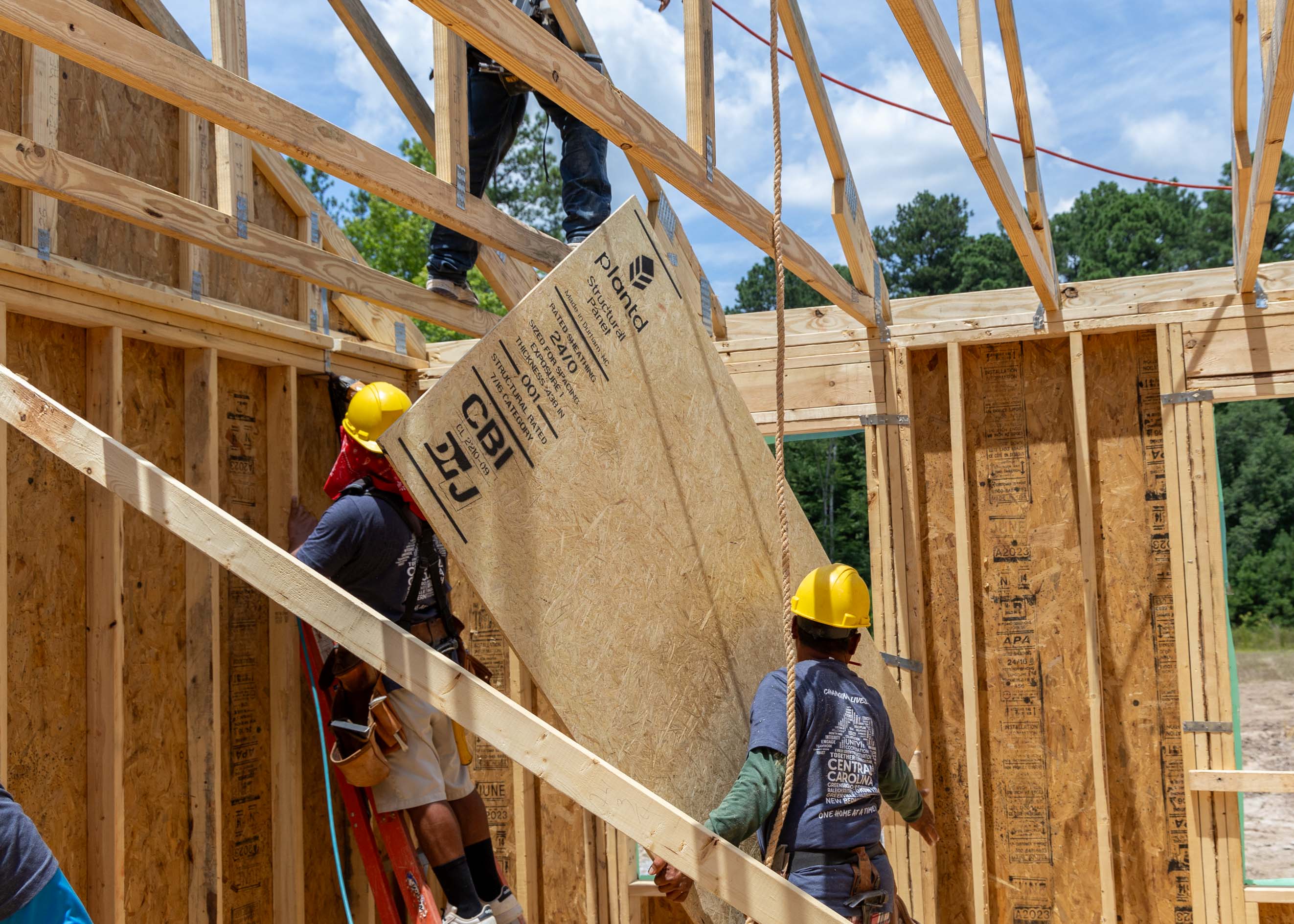
Q: Why wouldn’t you just use off-the-shelf manufacturing equipment for making engineered wood products?
Nathan: The cost to entry. These machines that you need for making OSB can be as expensive as $400M, while we can redesign these machines for a fraction of that cost.
Huade: It would be slow too. It would take many more years than we have been in existence to set up our first production line. It’s hard to justify those two things in tandem as well. This is a cheaper, faster, and more efficient way to test and develop hardware than trying to buy something to fit the box.
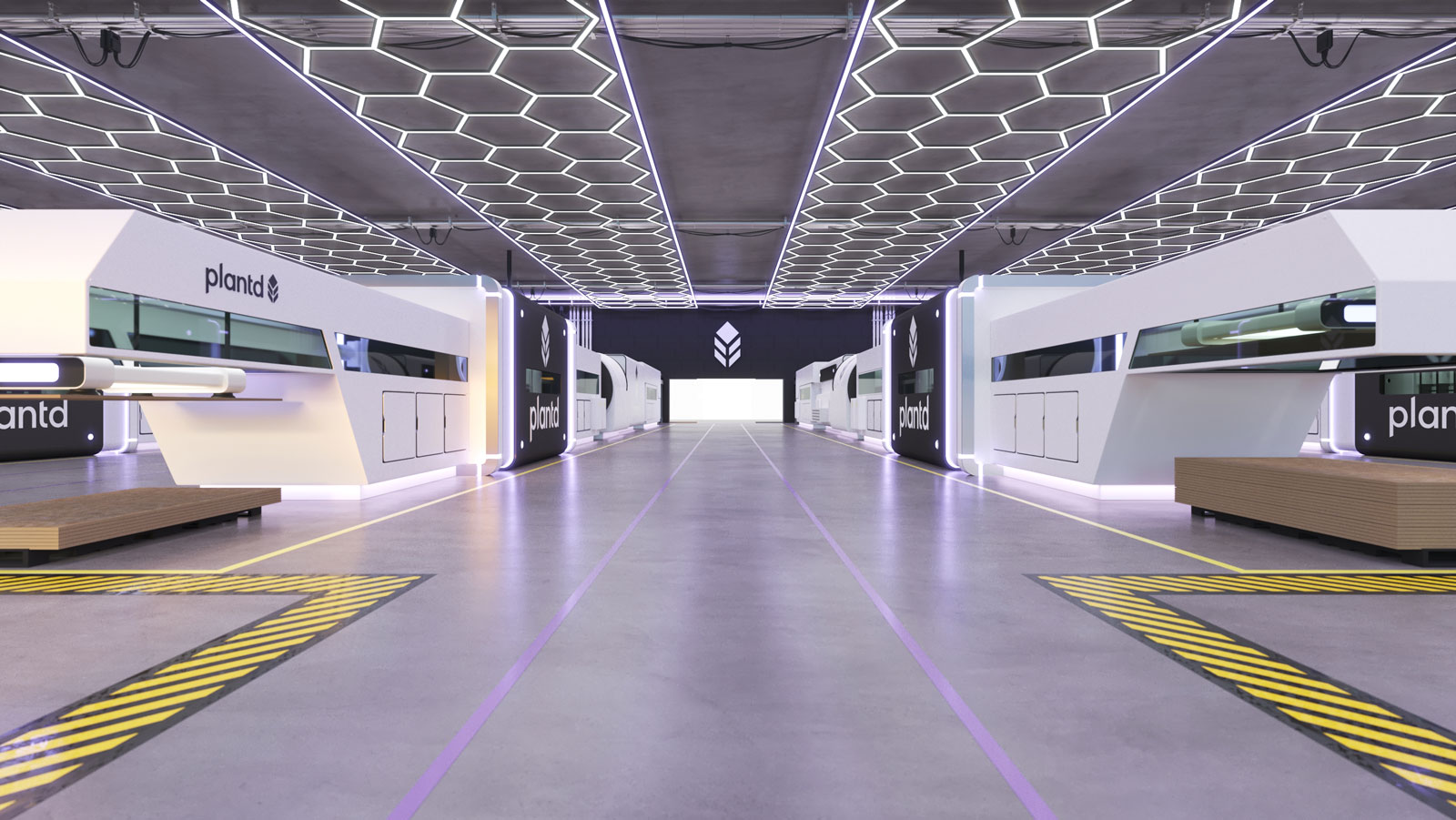
Q: What makes working with perennial grass different than working with wood?
Huade: One of the core technologies of the grass panel itself is how we process it and how the grass is a stronger and denser fiber than wood from trees. Morphologically, it’s very different to use grass instead of trees. Everything has to be designed to process and use stalks of grass instead of logs.
Nathan: The biggest difference is how our grass grows back far faster than loblolly pine. Managing a supply chain for the production of a fast-growing plant is much harder than managing the logistics for trees.
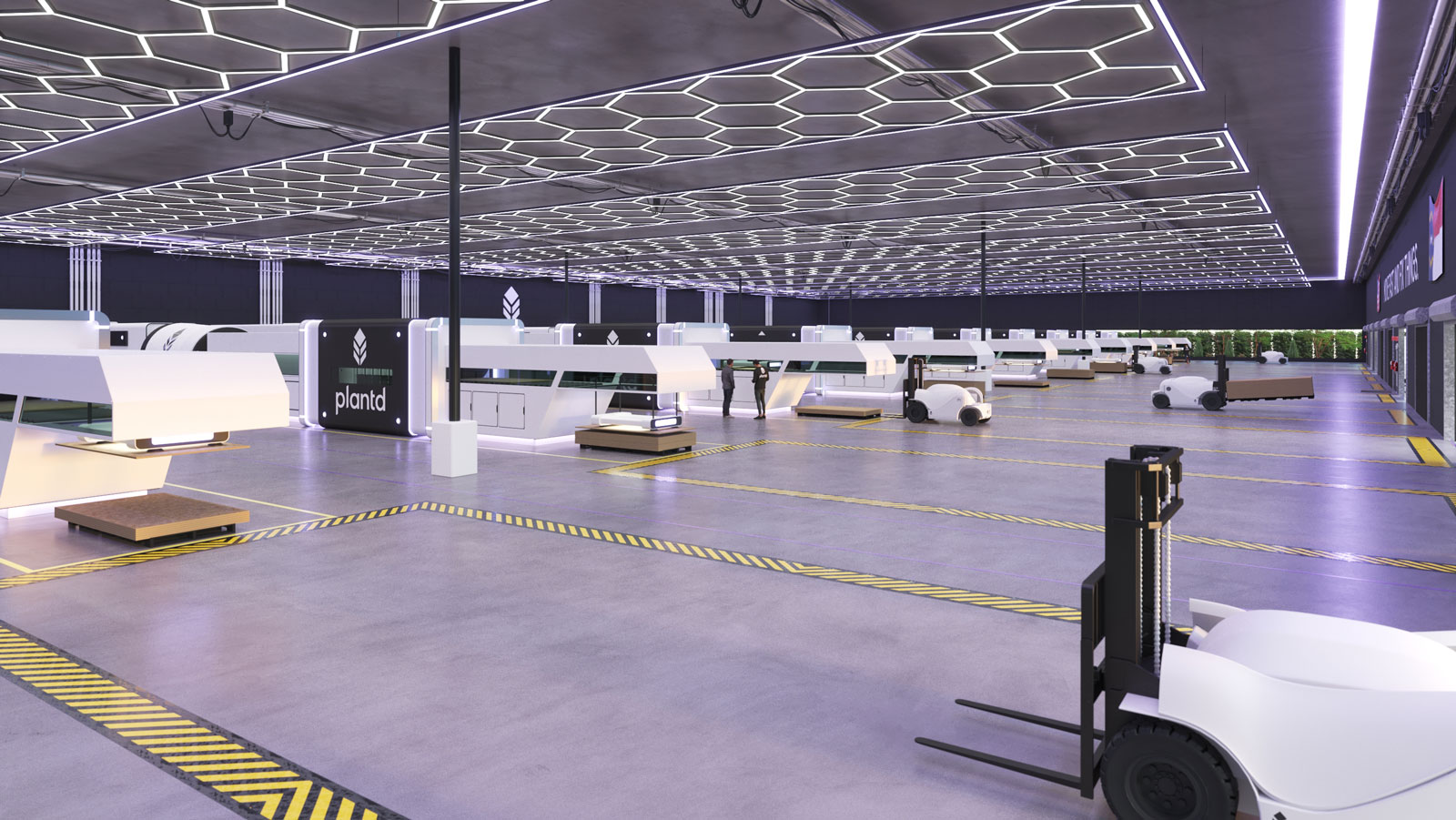
Q: What type of team does it take to design and build Plantd’s factory?
Huade: We run our Engineering Team like a race team. Our production team comes from traditional heavy construction. We look for a culture that’s close to a team that designs and builds race cars rather than a traditional engineering firm. At Plantd, we work closely in a very dynamic environment to solve problems quickly rather than to instill a bureaucratic structure, which trades off speed for risk aversion.
Nathan: It takes free thinkers. It takes people that are not tied to any one idea or concept. We need people who can look at a problem and create a novel solution to solve it. People who do not have a lot of experience in the engineered lumber industry are actually preferred to people who consider traditional constraints.
Q: How has working at SpaceX changed your engineering methodology? Do you apply SpaceX methods at Plantd?
Huade: The fundamental engineering methods that we apply here are exceptionally similar to the SpaceX methodology. The SpaceX methodology is a five step process:
1. Make requirements less dumb
2. Design out hardware, delete the part if you possibly can.
3. Make the part as efficient as you can
4. Go as fast as you possibly can
5. Automate
We’ve effectively done 1-4 throughout our journey so far at Plantd and will focus on the last step, Automation as we build our piilot production line.
Nathan: SpaceX developed my engineering methodology… and hell yeah, we apply it here at Plantd! Effectively, everything we do here is based on that. Everyday that I come to work to think about our business, I think about how we would do it at SpaceX and apply it here. For instance, we have a customer-financed revenue model similar to what they do for the Falcon 9 rocket at SpaceX. They use revenue from the Falcon 9 to build another one, just like we can use our production lines to build more.
Q: Why hasn’t anyone done this before? (This means, creating a new production technology for a new type of building material made of grass)
Huade: People have tried and failed. The inventor of the diesel engine couldn’t make his invention work. He died, and then people after him were fortunately able to make it work. There’s a time and a place for every innovation. And since the market is demanding a change, we seem to be at the right time and the right place.
Nathan: The reason why nobody would ever want to do this is because building an entirely new agricultural supply chain is incredibly hard. The barrier for entry is the time, the manpower, and the knowledge that goes into creating a new raw material from scratch.
Q: What drives you to build the factory of the future? Why do you come to work everyday?
Huade: For me personally, there is nothing quite like seeing something come to life from nothing. I’m incredibly enthusiastic to have built this company from effectively nothing and see where it is every day. I come to work imagining where it can go in the future and I find that exciting.
Nathan: At SpaceX, we were working on something incredibly selfish, which is creating spaceships to leave this planet behind, effectively leaving billions of people to live in a problematic world. Instead of leaving this planet behind, at Plantd we strive to create a better home for humanity. I firmly believe in this Albert Einstein quote, “I believe we are here to do good. It is the responsibility of every human being to aspire to do something worthwhile, to make the world a better place than the one we found”. The fact that this team can solve one of the greatest challenges known to mankind excites me.