How Technology and Innovation are Transforming U.S. Home Construction
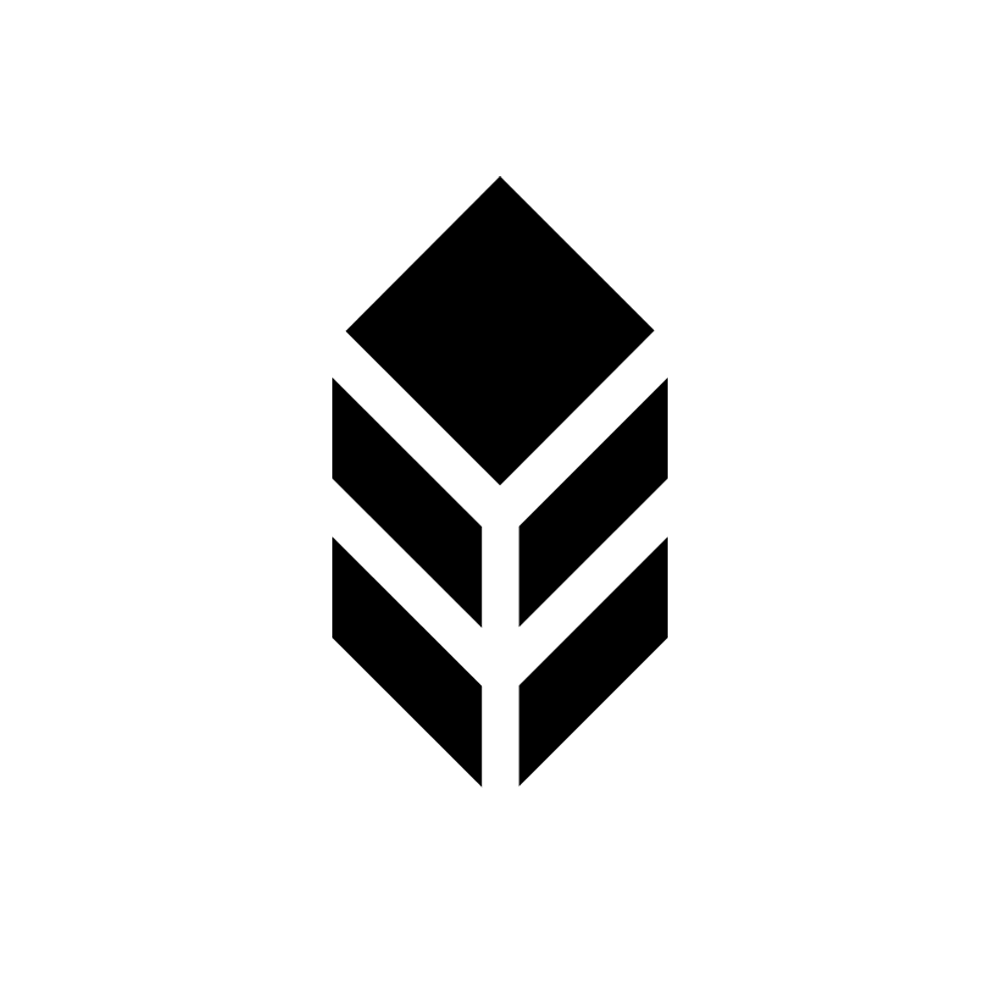
Dan Webb
/
10.26.23
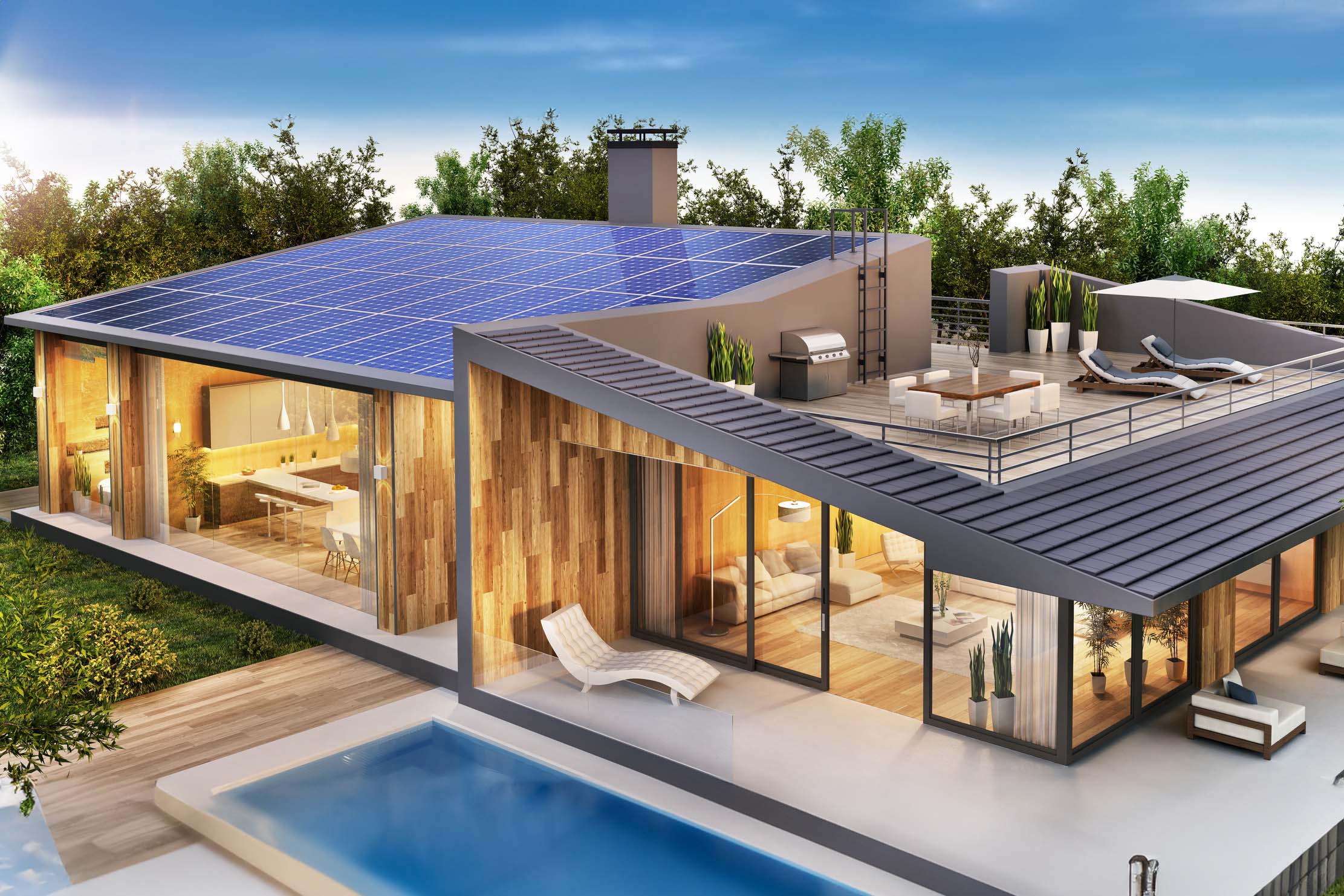
Single-family homes in the United States look very different than they did centuries ago, but at their core are still wooden frames with walls and roofs. In this blog post, we explore how technology and innovation are transforming American home construction and how new high-performance materials and building techniques are stepping up to the challenge of creating more sustainable, affordable, and resilient homes for the future.
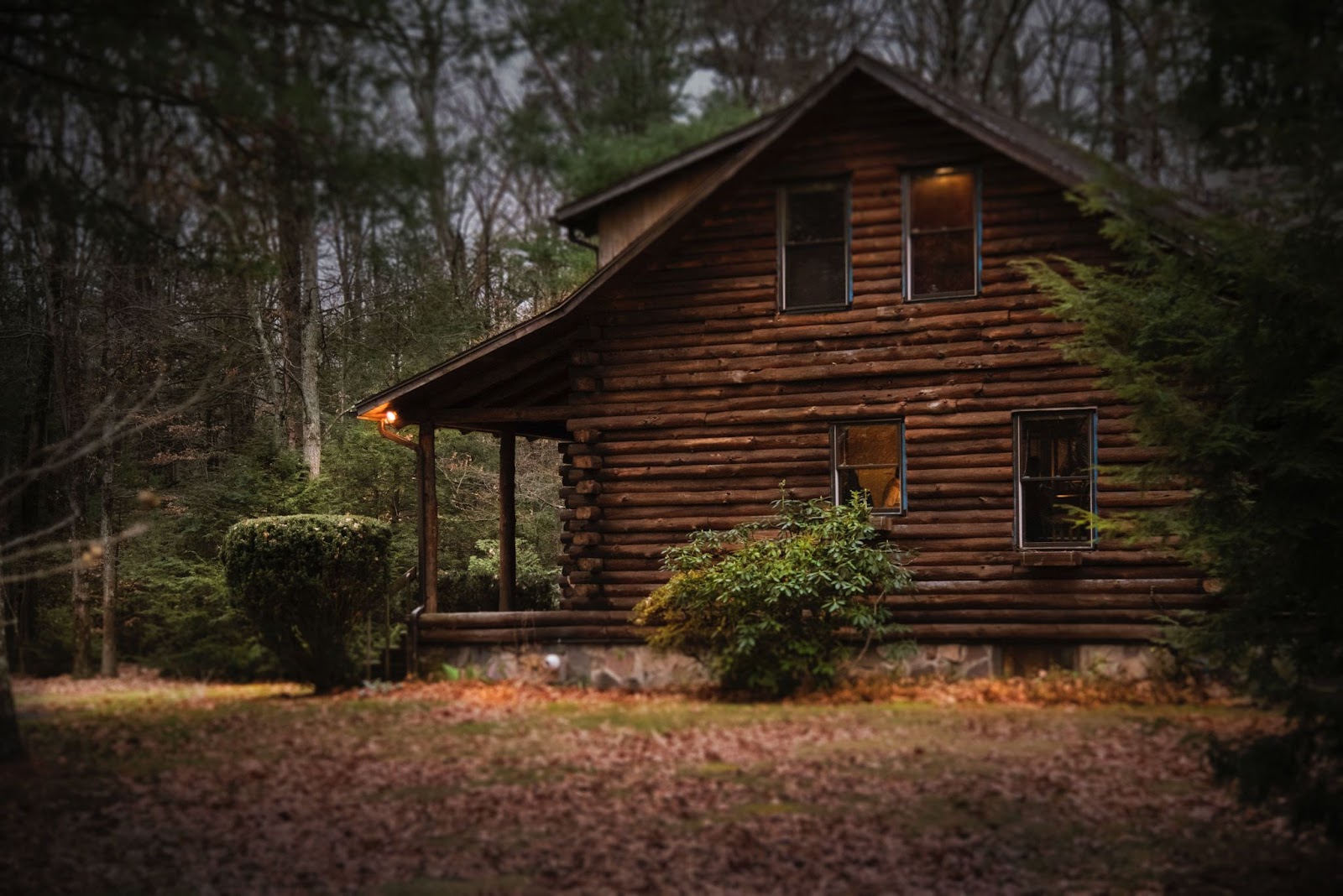
Building with an Abundance of Old Growth Trees
As far back as 1585, settlers built the first English colonial homes in North America with a construction technique called “wattle and daub,” where timber frames are lined by arranging sticks and filled with available resources, like mud, grass, and straw. Since it required only the most basic materials to build homes, this age-old building technology was standard among early settlers.
A wave of new European immigrants from countries like Germany and Switzerland, plus an abundance of old-growth timber across the American subcontinent, popularized another homebuilding technique: log construction. A log cabin has walls built from unmilled logs that are notched and stacked to create thick walls of overlapping timber.
With the rise of industrial sawmills in the mid-1800s came lumber cut by machine instead of hand. Dimensional lumber, like beams, planks, and boards, allowed carpenters to frame homes using 2x4 studs and cover exterior walls in softwood panels called clapboards.
In the 20th century, wood construction techniques stayed largely the same. Carpenters and builders changed from old framing techniques in favor of new ones. One instance is balloon framing, where the framing of walls extends from the base of the foundation to the roof. This technique became less popular in favor of platform framing, where builders construct wall framing from the bottom to the top of each floor and then to the roof.
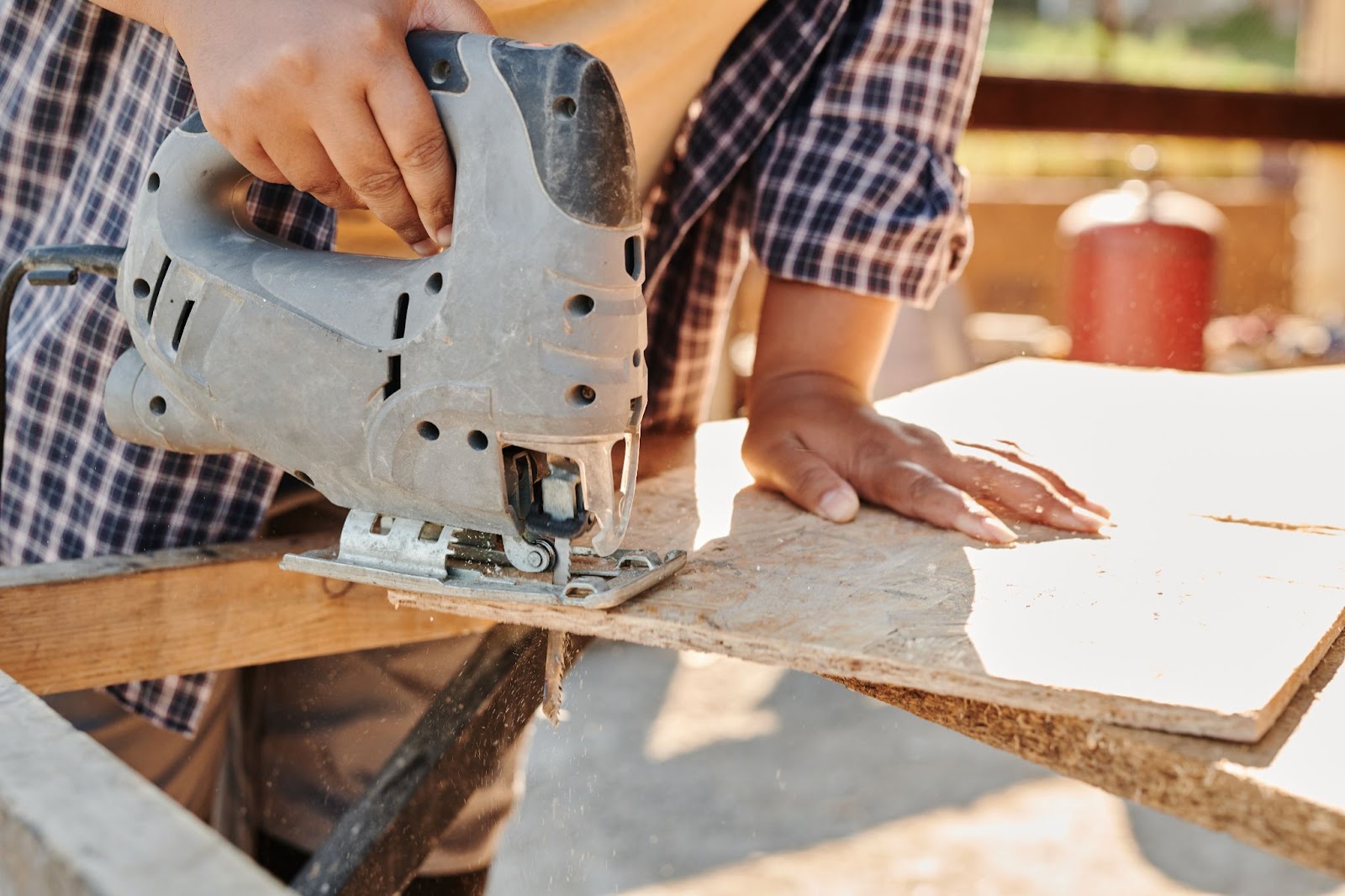
From Wood Waste to New Home Construction
By the 1960s, the large trees that comprised old-growth forests became depleted, causing another shift in material use toward engineered wood instead of wooden boards. Weatherboard and clapboard sheathing became less popular in favor of a new product called plywood, made from laminating veneer strips in a crossed pattern.
Increased demand for building materials led to the invention of materials made of sawmill scrap. In the 1980s, Oriented Strand Board, or OSB, became popular across the United States. OSB is pressed from three layers of wood strands, oriented in alternating directions, similar to plywood. According to the United States Department of Agriculture, the invention of OSB meant that 80% of the wood in the country’s forests could now be processed into marketable products.
The Future of Home Construction
In 21st-century home construction, the bill of materials is primarily the same as the homes built in the 1980s. Most homes today are made from stud framing and wood composite sheathing.
Much like the scarcity of old-growth wood created an opportunity for a shift in construction technology, 21st-century problems create opportunities for innovation. As the U.S. contends with challenges like housing affordability and climate change, new construction technologies may change what or how Americans build homes.
Offsite construction poses the potential for solving housing affordability through operational efficiencies. Startup companies like BotBuilt,Blueprint Robotics, and Reframe Systems are automating construction to create homes and home modules to install later on-site.
Whether building on-site or off-site, builders need materials that emit carbon dioxide in their manufacturing processes. Foundation materials like concrete and brick, plastics like vinyl and polyethylene, and timber products like 2x4s and plywood are all contributors to climate change.
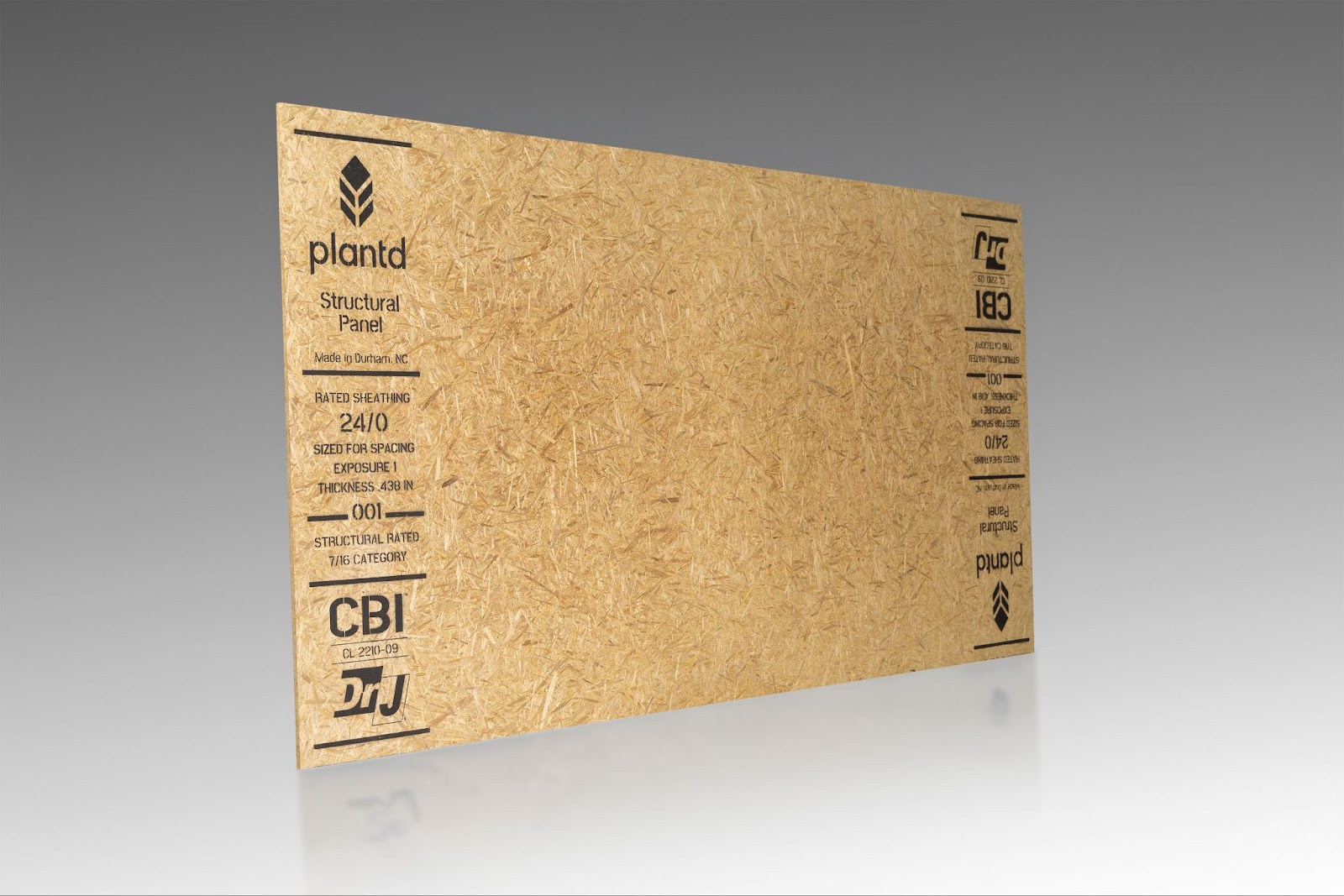
The Next Generation of Materials
A solution that brings new high-performance materials to market is Plantd Structural Panels. These panels are installed just the same as the sheathing materials that homebuilders have used for generations. Instead of trees, we make Plantd panels from tall, rapidly regenerative grass that grows back every year.
Our unique technology allows these panels to perform better against severe weather conditions like heavy rain and wind. Plantd panels are 1.4x more robust than legacy materials like Oriented Strand Board and are 2x more moisture resistant.
Whether it be opportunities, like a new abundance of raw materials, or challenges like climate change, humankind has developed new technology to continue to build homes and shelters for all. At Plantd, we’re tackling the challenge of climate change by creating carbon-negative building products. That means every panel exiting our production facility sequesters carbon dioxide emissions removed from the atmosphere. That means together with homebuilders, we can help solve the climate crisis by building more, not less.
Learn more about our first carbon-negative product, Plantd Structural Panels.