Building the Future, One Machine at a Time
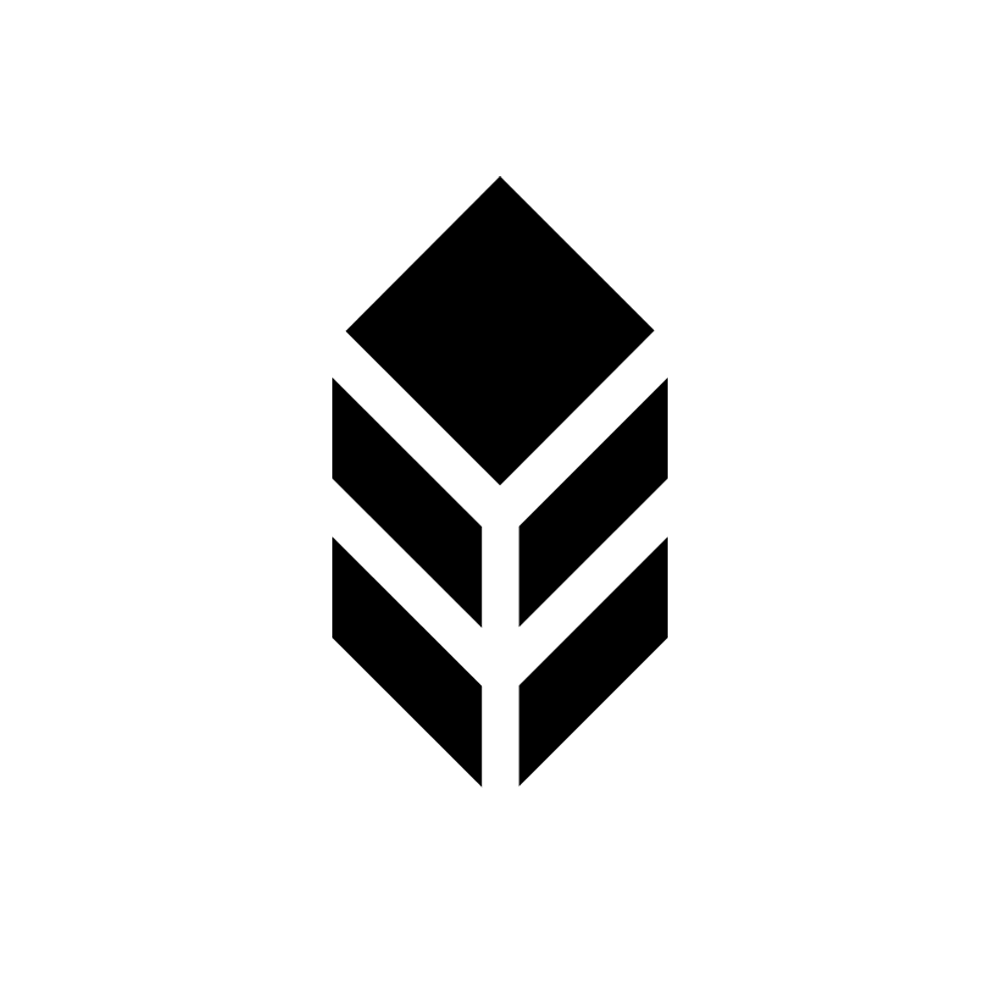
Josh Dorfman
/
11.30.23
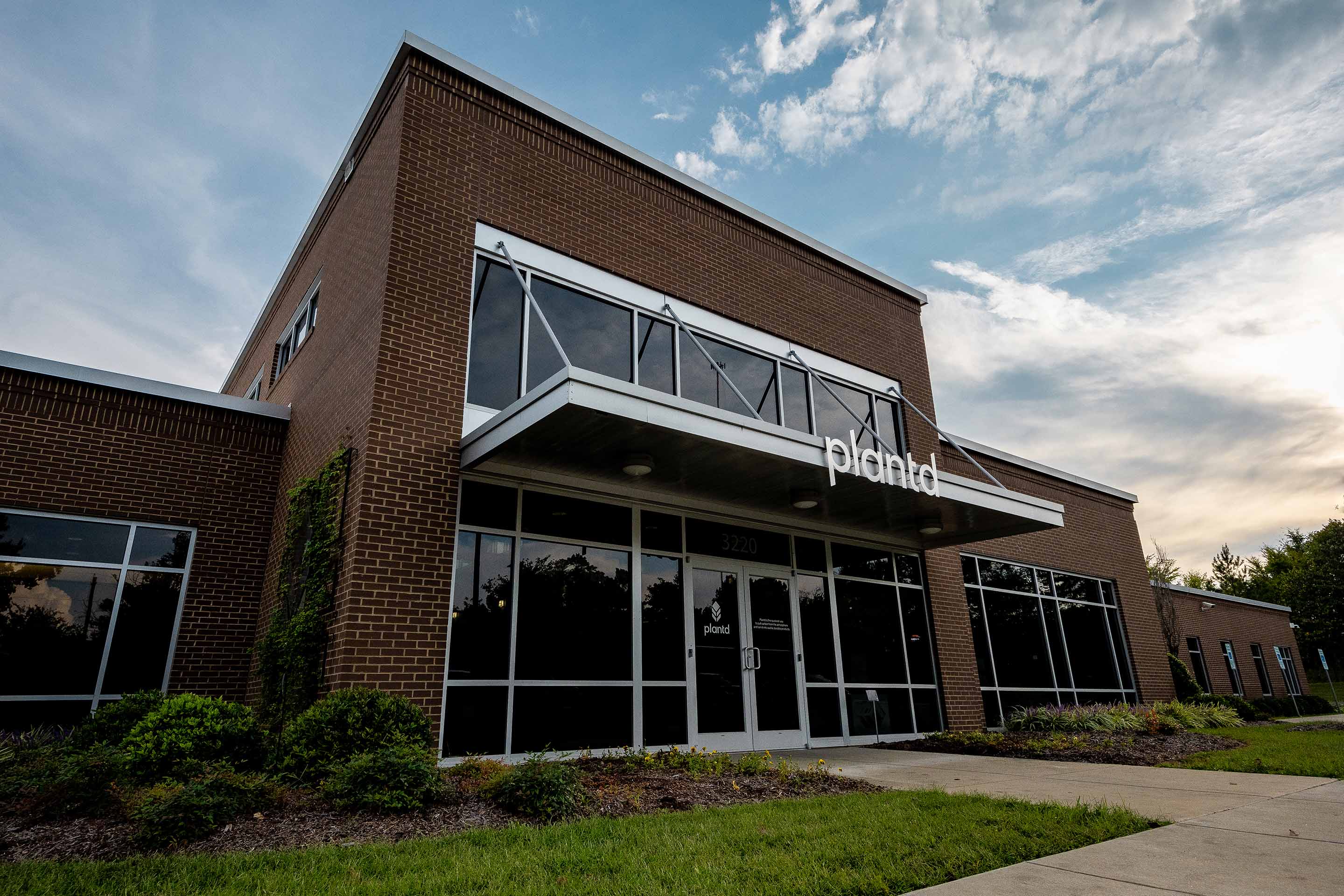
Visit any factory in the United States that makes structurally engineered panels for homebuilding, and three things stand out.
- Their scale is enormous, like the size of a small town.
- They have massive smoke stacks emitting carbon dioxide.
- The machines for their assembly lines largely look the same.
To succeed in our efforts to rapidly draw down carbon dioxide from the atmosphere and transform it into useful, durable building materials, we knew another approach was required. We would have to redesign the entire production system.
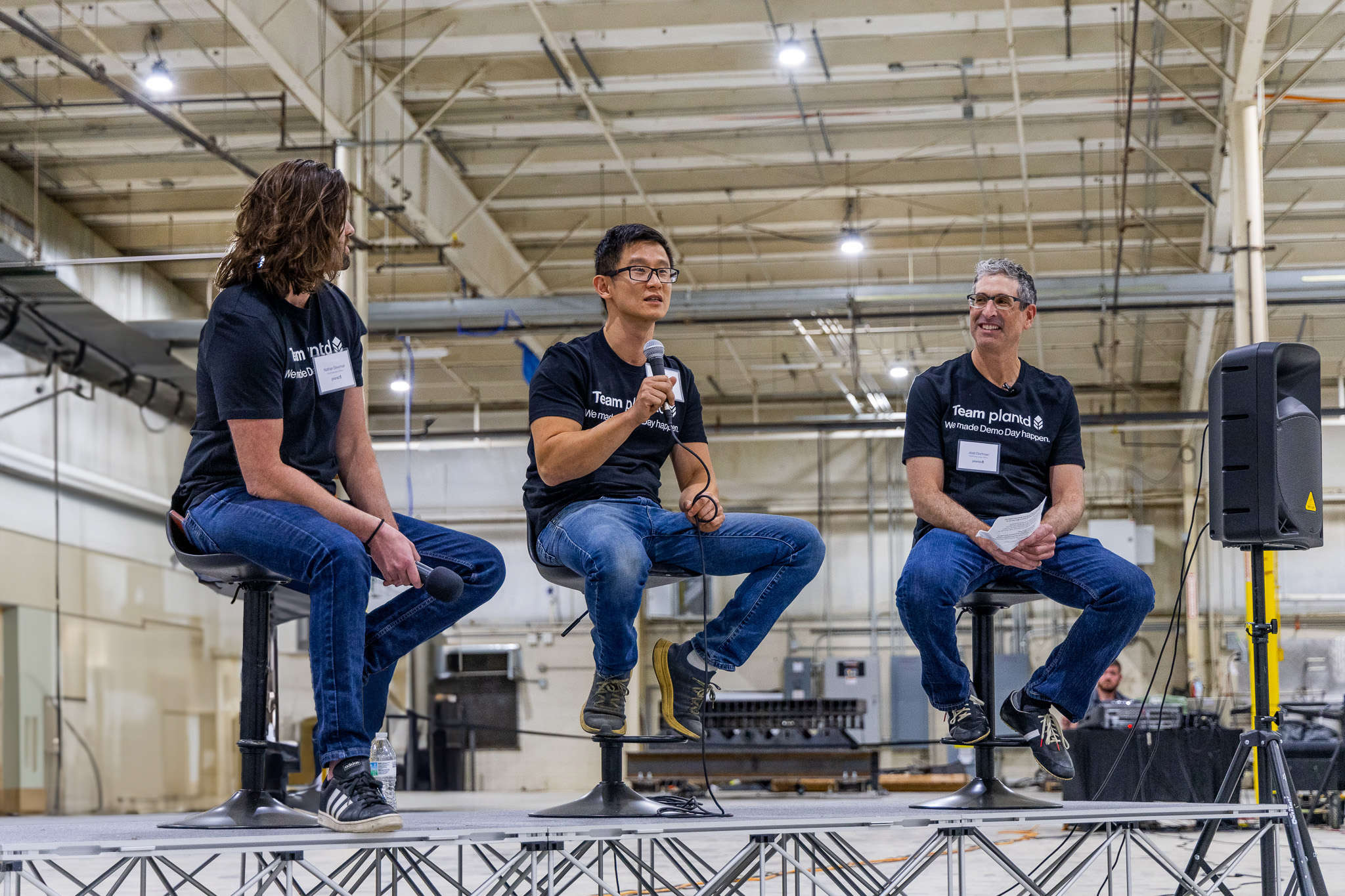
This month, we invited Plantd’s investors and industry stakeholders to our first Demo Day, where we unveiled our pilot production technology and presented our vision for the Factory of the Future. Our guests viewed how we’ve built our machines, downsized their scale, and eliminated the smokestack.
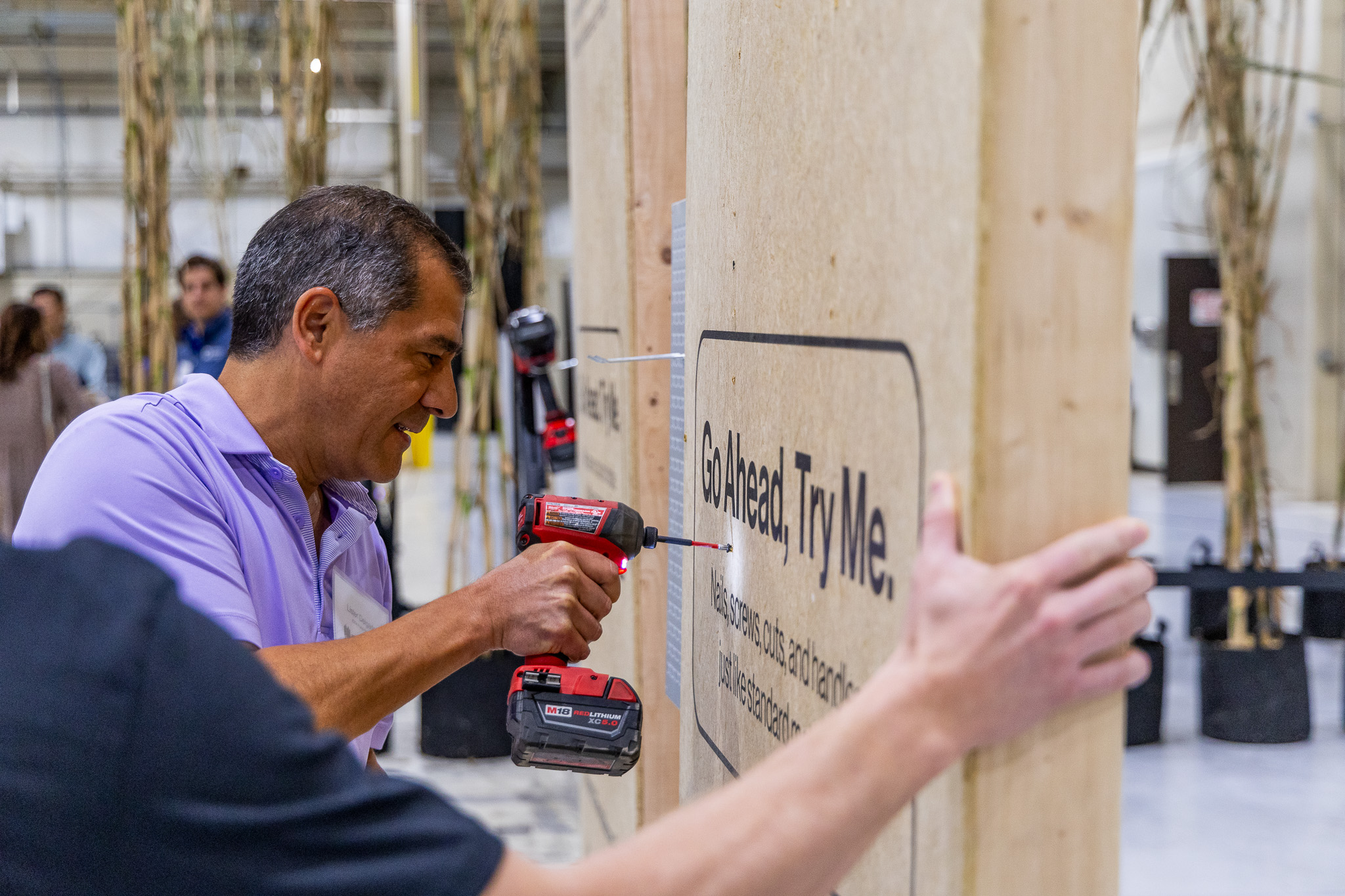
When we hire engineers and production technicians, we tell them they are here to build the machines that will build the future. This is precisely what we are doing: one machine, one sub-assembly at a time. However, at Plantd, time itself is in short supply. We know the future can’t wait, which is why our mantra is Move Fast and Fix Things.
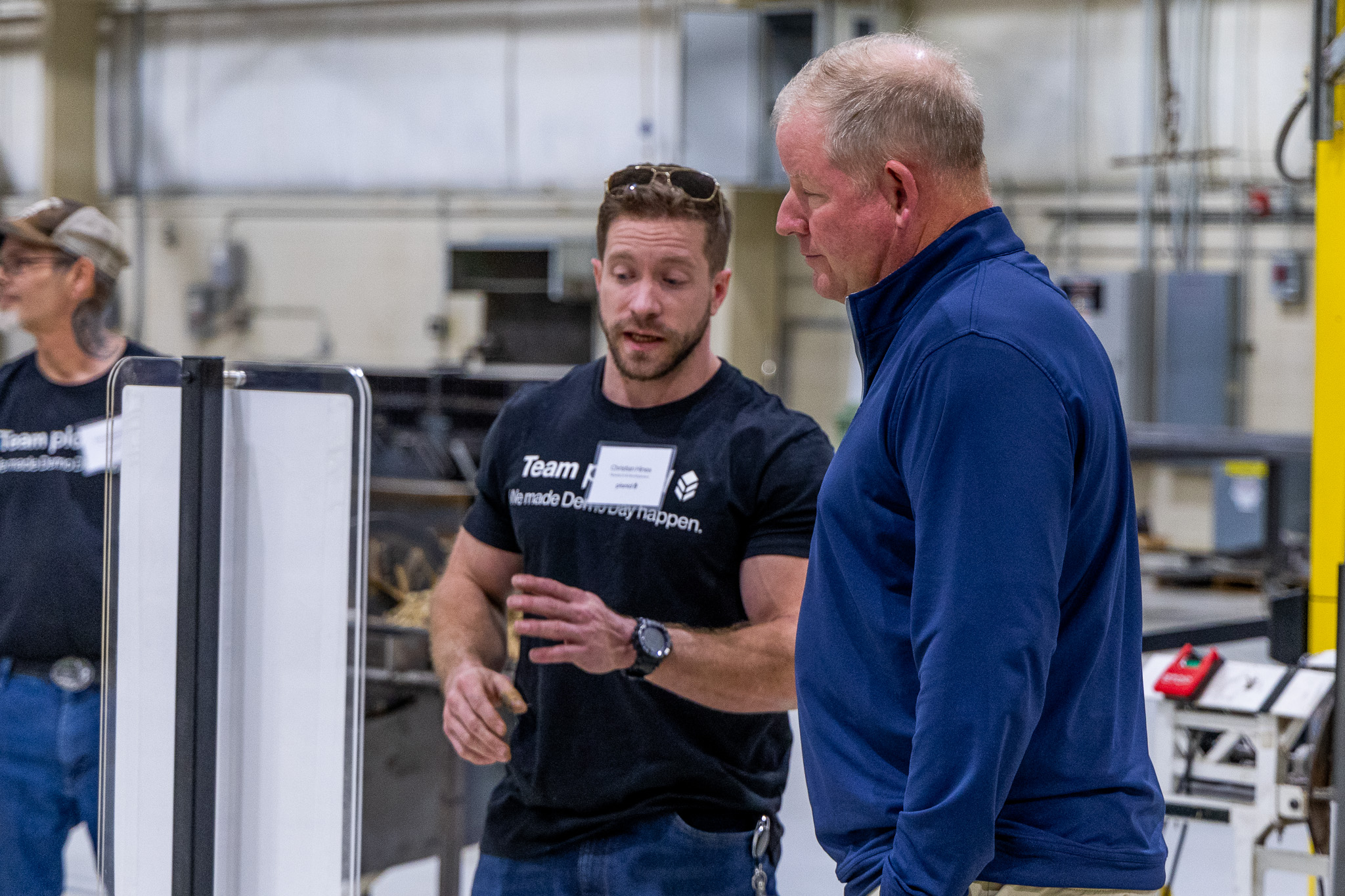
Since founding Plantd in 2021, we’ve stuck to this approach, steadily, methodically, and rapidly progressing through numerous machine designs. With each new machine iteration, we collected data and refined our approach, enabling Plantd to progress quickly from making sub-scale building material prototypes to full-size, code-certified structural panels.
When we moved in and repurposed a former tobacco products factory in Oxford, North Carolina, earlier this year, we knew we had found our home for the next phase of our growth.
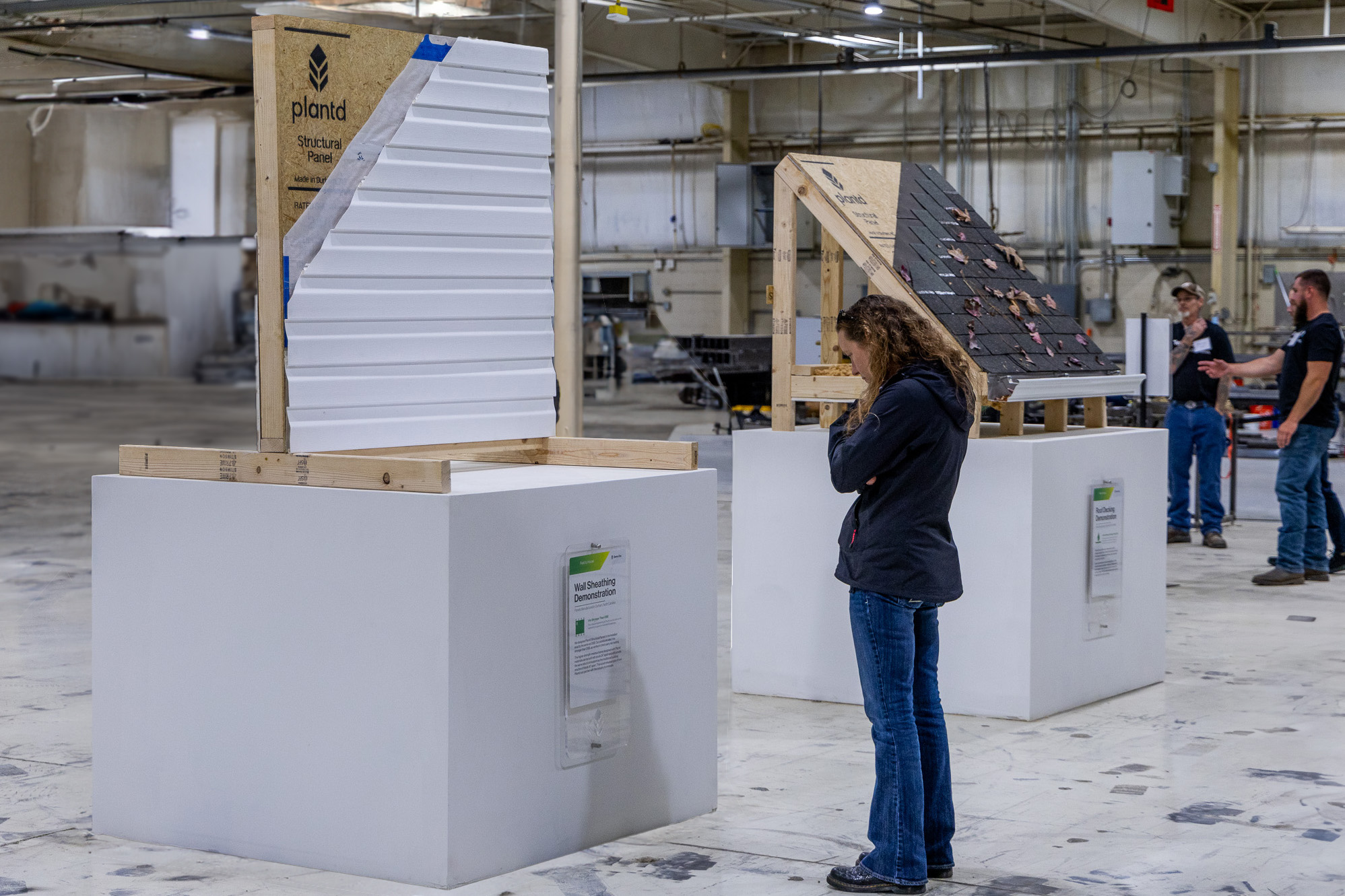
Our guests who visited this month received an up-close look at our machines. They met our team that designs and builds them. They experienced how our Factory of the Future enables us to cut carbon emissions and costs from the production of structural building materials, both of which are vital to solving 21st-century challenges like climate change and housing affordability. They heard how our modular, light-industrial production technology provides Plantd with the flexibility to shorten supply chains by locating our factories close to where homes are built, further curbing costs and carbon emissions.
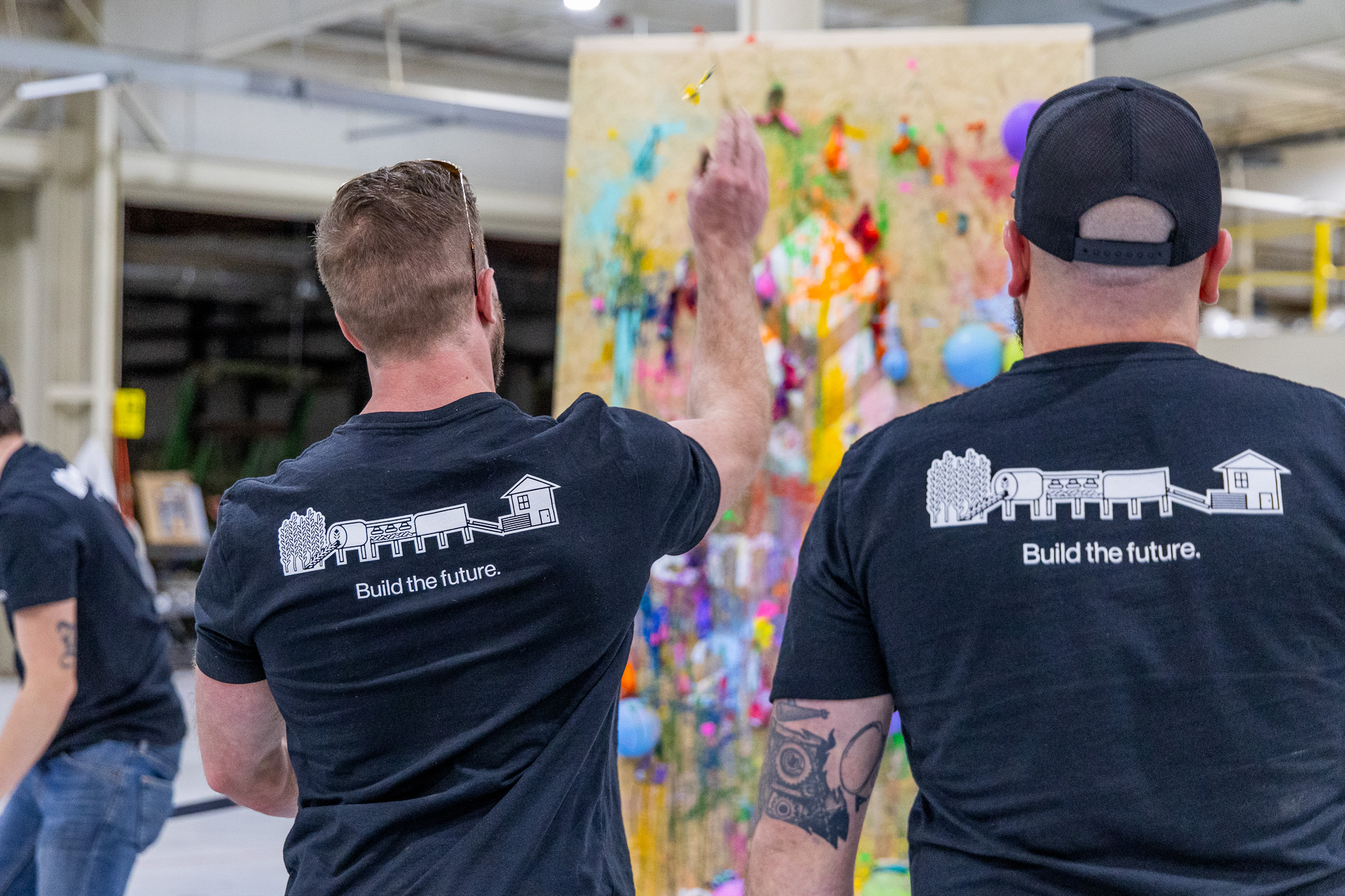
They heard firsthand what it means to all of us at Plantd to be on this journey. We are proud of how far we’ve come in only two years and recognize that we still have far to go. Yet, we know that the future of homebuilding runs through Oxford, North Carolina; in fact, we’ve repurposed to foster American innovation and build the future.